
How an Ex-Formula 1 Chief Mechanic Built the 2024 British Grand Prix Trophies
16 July 2024For the 2024 running of the Formula 1 British Grand Prix, Silverstone organisers commissioned local sculptor Alastair Gibson and his Brackley-based studio Carbon Art 45 to build a set of four bold new trophies for the iconic event. The ex-chief Mechanic at BAR and Honda is known for his use of car parts within sculptures, creative application of carbon fibre, and a deep-rooted understanding and personal history in motorsport, making him the perfect candidate for this important task.
With nods to sustainability, nature, Grand Prix heritage, and creative use of real parts from Formula 1 cars, the trophies symbolise the historical significance of the British Grand Prix, and what it continues to bring to the sport today.
In the end, a fairytale story unfolded over the weekend, as nine-time Silverstone winner Sir Lewis Hamilton took first place at the end of the race and, along with the Constructors’ trophy, both pieces returned home to the Mercedes team factory where Alastair once worked.
We caught up with Alastair to learn more about his own relationship with motorsport, art, and his experience building the 2024 British Grand Prix trophies.
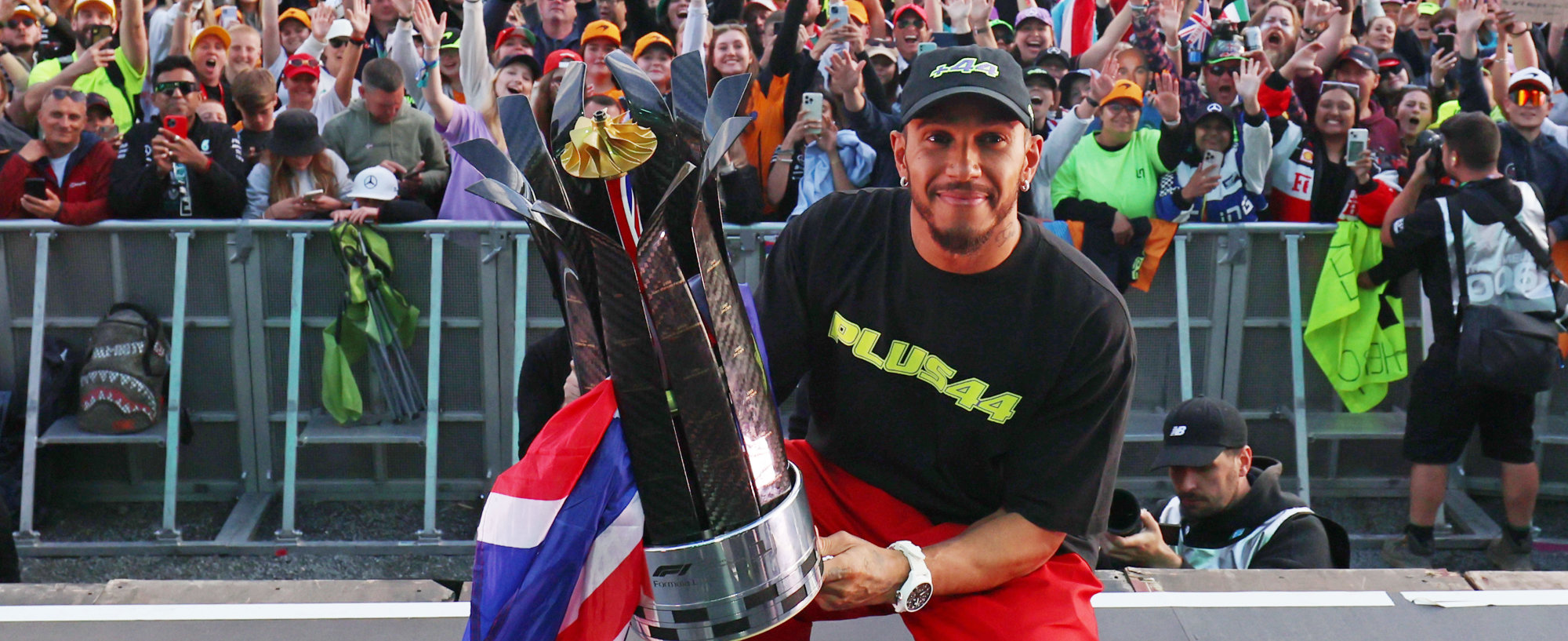
A career in Formula 1
Coming to the UK from South Africa in 1986 with the goal of getting involved in the country’s thriving motor racing industry, Alastair started out working in lower Formulas - Formula Ford, Formula 3, before quickly working his way up to Formula 1 where he worked at Benetton when Michael Schumacher was winning his first World Championships.
“I went in with a very experienced team and I think it really helped me a lot. They were World Champions and I learned from World Champions.”
Gibson stayed with the team until 1997, when he left to become Chief Mechanic at newly formed BAR. While the team never shared the success of his previous employer, Gibson recalls the team spirit ensured it was a great place to work, “[they were] all a great bunch of guys, we all came into this big building, sat down, and were told our jobs. We just got on with it.”
He stayed with the team until 2008, by which time they had become Honda. “The only Grand Prix we won was in Hungary with Jenson Button.“Unfortunately, they won the Championship the next year with Brawn, but I wasn’t bitter. I enjoyed looking at the Grands Prix and seeing all the guys I’d employed and trained up.
“I was well into my sculpting career so just enjoyed watching it.”
Transitioning from Formula 1 mechanic to sculptor
Alastair always had an interest in taking something made in 2D-space and bringing in a third dimension. Looking back, he recalls how his parents’ holiday cottage on South Africa’s coast had a role to play in nurturing his love of sculpting. “I used to go and walk around the rocks to pick up dead fish and got involved in sculpting them from wood.
“The fishermen used to catch quite large sharks and bring them up on the beach in the ‘70s. I used to cut the jaws out, dry them on the roof of the cottage, and mount them on wood.
“I’d take them back to Johannesburg, where we lived, and would sell them to my mates at school.”
When he moved into Formula 1, Alastair saw another opportunity to turn what many considered junk into art.
“Initially when I worked at Benetton, I walked into the stores at the end of the season where they were about to chuck all these beautiful bits of titanium away, and I held them in my hands.”
He took them home to South Africa, “mostly to show my dad – he was a race car mechanic in the ‘60s. He was absolutely amazed at how far the whole Formula 1 engineering had come.”
The idea for using them came from a dream where he realised how these intricate parts could transform sculptures.
“I thought ‘that would be a great set of gills for a shark’, or ‘that would be a really good aerodynamic bit I could put on the side of a fish.’”
From there, he continued to work around his renewed love of sculpting, selling his sculptures while working in motorsport. Eventually came a time in his career where he didn’t want to do it anymore.
“I think the older you get in a job, the more you really appreciate time and how precious it is. And I just thought I had something else inside me rather than working on Grand Prix cars, so I became a sculptor.”
Alastair left the world of Formula 1 in 2008 to focus on becoming a fulltime sculptor.
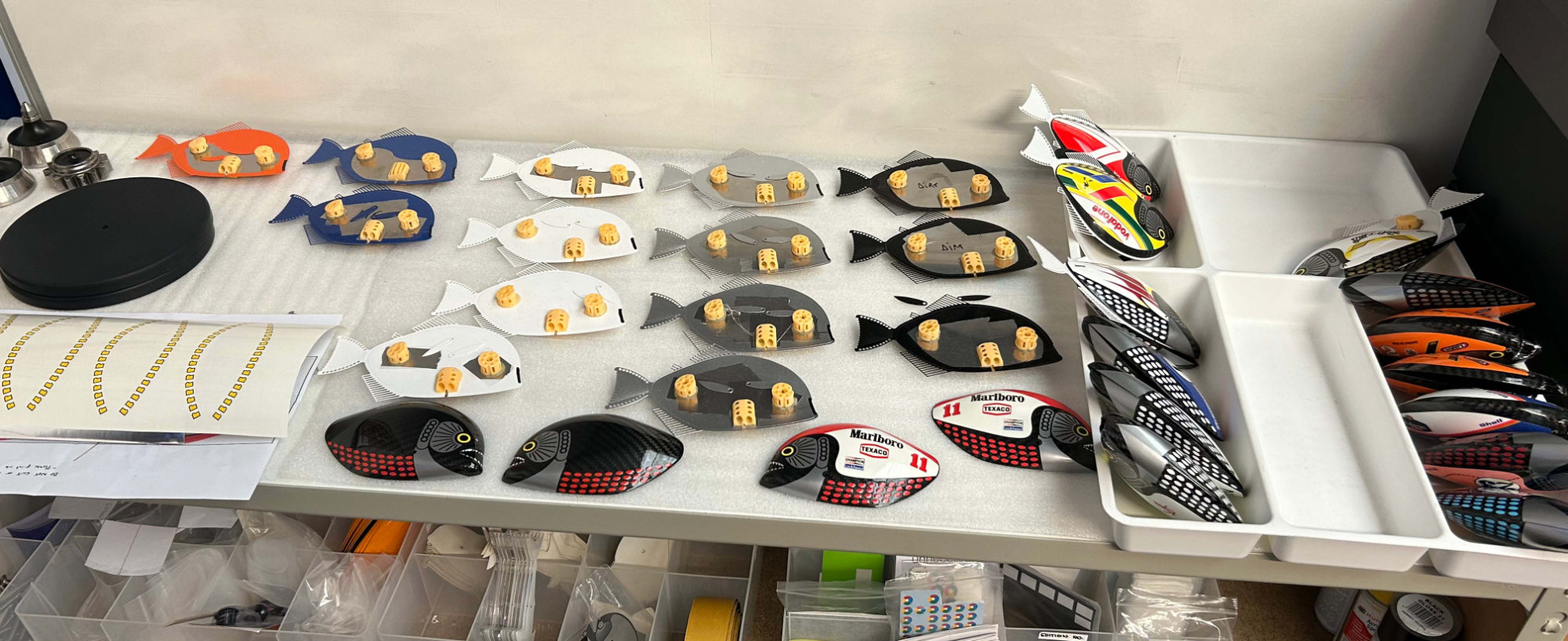
How the 2024 Formula 1 British Grand Prix trophies were built
With Alastair’s history using car parts in his sculptures, it felt only natural to continue this theme within the design of the Grand Prix trophies. From the beginning, he had a vision to use sustainable materials and provide new life to old Grand Prix car components, while making nods to the history of Formula 1 and Silverstone’s heritage.
“In the early days of racing, when they won a race, they would give [drivers] a bouquet of flowers.
“There wasn’t a wreath, there wasn’t a trophy – they just gave them flowers.”
Alastair chose to incorporate this history into the design, using car parts to form the shape of a flower.
“The flaps of the Grand Prix car are like the leaves that come around the flower. The turbo charger impeller is the centre of the flower.”
When the design and ideas were established, Alastair’s attention turned to how he would be able to bring this vision to life.
“Once I had an idea like that in my mind, I thought the best thing to do would be to create a 3D printed version. I used a company I’ve worked with a lot [before] on other projects. In fact, they’re just across the road from the podium at Silverstone.
“I gave them all the drawings and they 3D printed it. This helped me massively to check out the size, see the proportions, and calculate the weight of the trophy.”
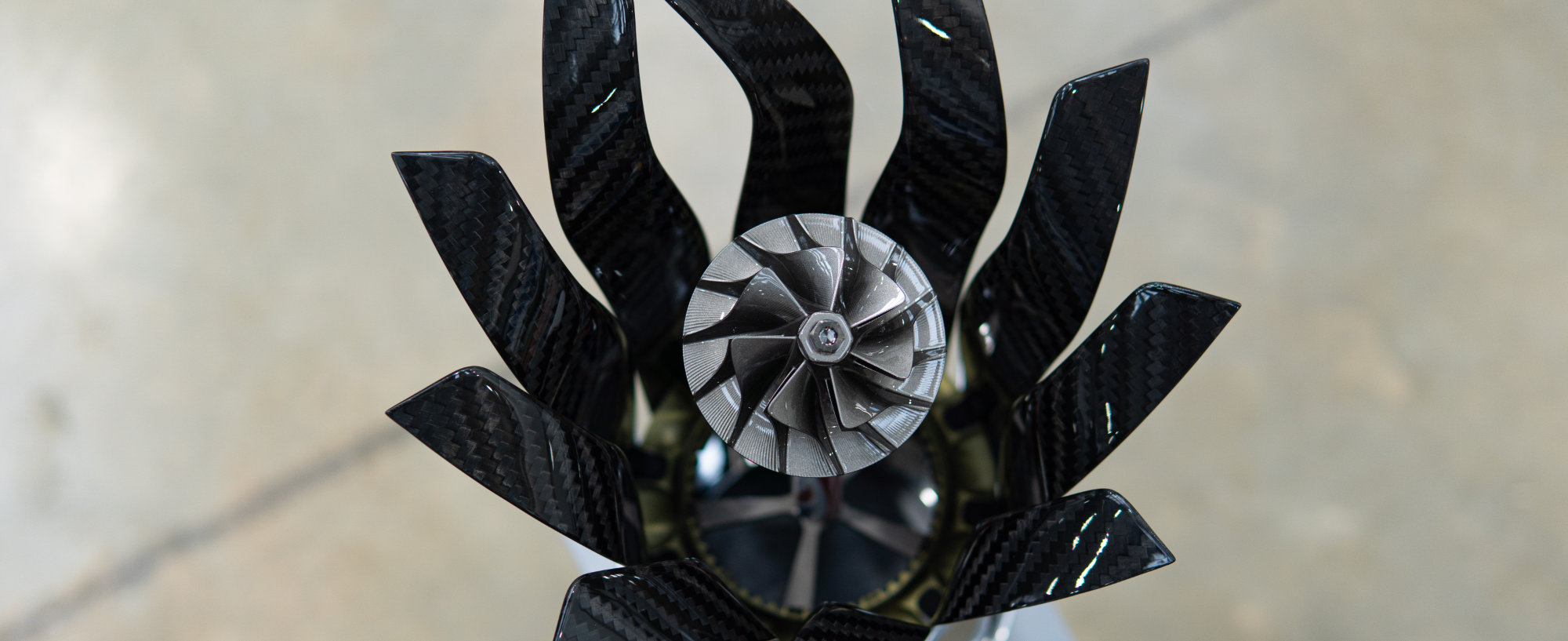
After that, Alastair had to then source all the car parts needed for the trophy.
“We actually use parts that have been in a Grand Prix at some point in their lives.”
Then came assembly. Calling on his team of five others at his studio, they all worked together to build and assemble the final parts of the trophy. The team work together to ensure that nothing is missed.
“They comment on things I might oversee in my haste.
“For example, when they’re celebrating on the podium [we had to think about] how they would hold the trophy in one hand and a bottle of champagne in another. Is it going to be strong enough to be held by one of the single carbon fibre flaps?
“Also, if one of the drivers decide to throw it in the air, where is the centre of gravity? If the centre of gravity is halfway up, it’ll start cartwheeling in the air – but if it’s got a balanced ratio, hopefully it’ll come down the way you threw it up.”
Alastair hopes that drivers and teams appreciate the thought that has gone into designing and building the trophy, and notice the subtle parts that nod to Formula 1 heritage.
“Hopefully the drivers and teams who get these trophies will look at it and get the big picture and the Silverstone heritage with the names on it, front wing flaps, the turbocharger impeller, and think ‘wow this has really had some thought put into it.’”
Alastair Gibson on being picked to build the trophies
Being asked to build the trophies for one of the biggest sporting events in the UK is a big task, with not just the drivers and fans at the track who will see your work, but millions worldwide. On top of that, an event as historically significant as the British Grand Prix adds an extra layer of pressure to deliver something unique but stays true to the race’s heritage.
“I felt really honoured that I’ve been given the chance to do this.”
Alastair felt it was a huge challenge, but one that he was up for taking on. When it came to creating something unique for this event, he had big ideas.
“I wanted to make my design very interesting and more intricate than other designs I’ve seen at previous Grands Prix.
“I wanted to use parts from the Grand Prix car in the same way I use parts from the cars to build my sculptures.”
As for the brief, there was no specific direction provided, and Alastair was given freedom to design and build the trophy he wanted, the only ask being that sustainability sit at the foundation of what was built. Fortunately, Alastair’s expertise re-using parts in his work helped ensure the trophy maintained its sustainable credentials.
“The task was colossal, but also really interesting, because no one really gave me any direction. They gave me a clean sheet of paper.
“The difficult thing was the timescale. Not knowing until about two months before that I was actually doing it.”
“But I was overwhelmingly excited that I’d been given the chance to build the four trophies for the British Grand Prix.”

How sustainability guided the design and construction of the Grand Prix trophies
Sustainability is a key theme in this year’s British Grand Prix trophies. Re-using old car parts from F1 cars, a more efficient manufacturing process, and recyclable and lower impact materials were all key in its construction.
Alastair has a keen interest in the natural world, where his sculptures mostly resemble objects and animals you’d find in nature. While he admits he’s “not even a grain of sand in a big beach”, everything he does, he does while limiting waste and resource use.
“We like taking all the products used to make the sculpture and when we’ve finished curing it, take those products and put them inside the sculpture so they don’t go to landfill – they live inside the sculpture for its life.”
“People appreciate good engineering, and if we can do good engineering and look after the planet a bit too, then it’s got to be a way forward.”
The trophy mock-up was constructed using a nylon-based 3D printing process which produces virtually no waste. In typical 3D printing the support structure is cut away and wasted when the product is extracted.
“The system we used, the material [itself] acts as a support structure. And when you break it out of the ‘cake’, which we call it, all the leftover material is used again in the next 3D print.
“The only things we took out of the cake were the parts. The rest of the cake would’ve been used for another job or client.”
When asked why sustainability is so important to him, Alastair stresses the importance of education to young sculptors and artists.
“The big thing is education to young people. Young aspiring artists might look at these and think that even though it’s sustainable, it can still be beautiful, and well-engineered and thought out.”
Waiting 20 years to build a Grand Prix trophy
Having worked in the world of Formula 1 until 2008, Alastair understood the importance of Grand Prix trophies and admired the time and effort put into them. When asked how long this idea had been in his mind, Alastair stressed that it’s been a long time coming.
“The idea has been in my mind for a while. Ever since I was in Formula 1 and one of the drivers we were running got a podium. And I went up to see my driver on the podium I thought, wow, wouldn’t it be cool to design one of the trophies or be involved in designing one. A bit of a dream for me to do, so 20 years.”
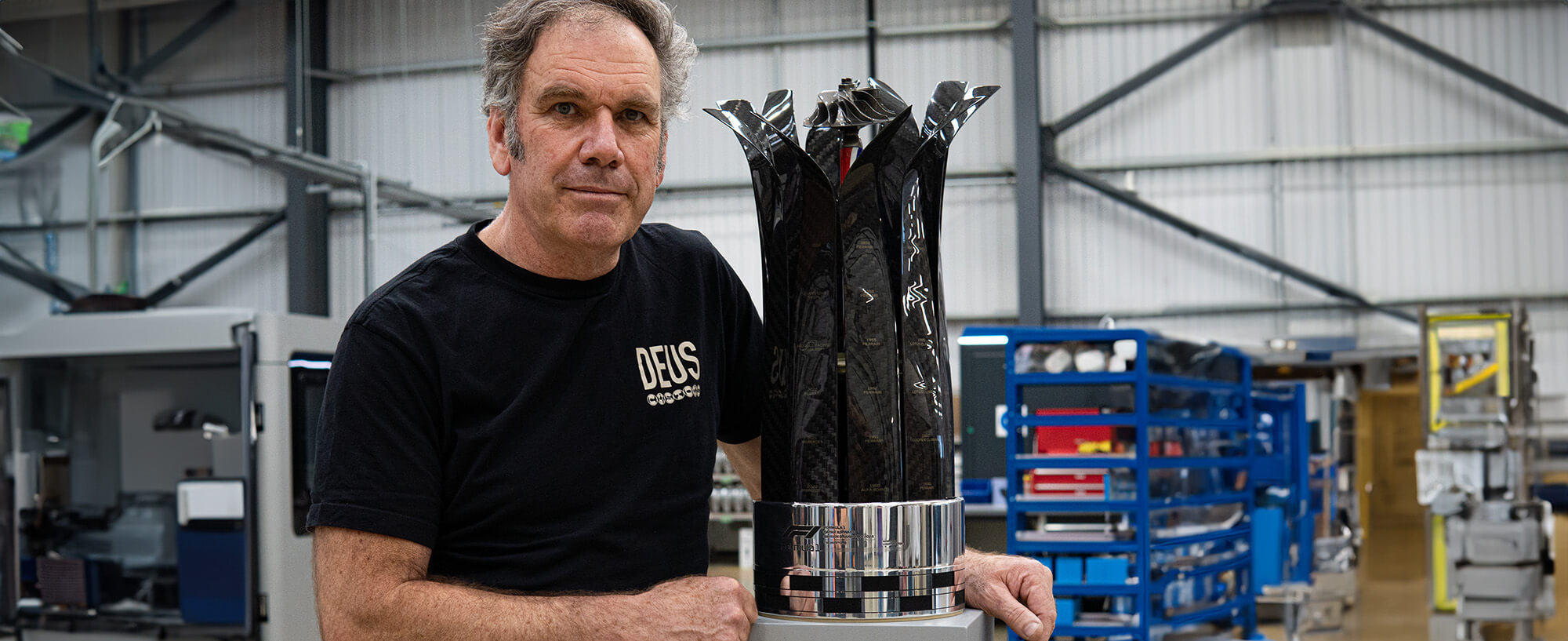
What are the limitations on Formula 1 trophies?
The 2024 British Grand Prix trophy designer had to stick to strict criteria controlling height and weight, but designers are given plenty of freedom when it comes to the trophy design itself.
“The challenge is created by the criteria to make the trophy. It’s valid – they want you to be free to do what you want to do; however, the winners and constructors can’t be bigger than 650mm, the second and third place 550mm, and it can’t weigh more than 5kg.”
Alastair also pointed out that while not mentioned explicitly, designers also need to consider how drivers will celebrate with their trophy, to keep both driver and trophy intact.
“Also, which they don’t put in the criteria, the centre of balance and sharp edges.”
On seeing the trophies presented to the winners
After the weekend, we caught up again with Alastair to get his reaction to the race result that saw two British drivers take the top spots, including Hamilton’s record-breaking 9th home win.
Alastair was able to get down to the podium to witness the celebrations first-hand. While a moment of overwhelming pride for the sculptor to see his trophies being admired by the winners, nerves were also high.
“The thing that amazed me was that they actually looked at the names, they sort of studied it.
“It was comforting for me, knowing that all the pain that went into putting the names on the trophies was actually appreciated.”
Back in the garages, the trophies were definitely a talking point for the teams.
“I’ve got a friend at Red Bull who said people were interested in the trophy.”
Seeing the trophies taken away back to garages was a relief, with anxiety somewhat heightened during the presentation.
“The underlying emotion was just relief and just to say [to myself] that they’re done, and they never fell apart with a flap coming off in someone’s hand.”
Seeing the trophies go out to drivers at the top of the sport meant a lot to Alastair, with two British drivers in Lewis Hamilton and Lando Norris, but also three-time World Champion Max Verstappen being passed the sculptures he had put so much effort into. To see “the all-time best British racing driver” Hamilton and “the next star race driver” Lando Norris receive his trophies was a moment of immense pride.
After the race he took a trip to the Mercedes garage where he had a catch-up with Hamilton’s race engineer Peter Bonnington and two mechanics he had worked with at Honda, who met him for an emotional chat and photographs with the trophy. Alastair recalls how it was great to spend time with the team and see just how far the technology has progressed since he left in 2008.
“It meant quite a lot to me actually; it was really nice.”
He followed up with a trip to the Mercedes factory in Brackley to meet more of the team, check on the trophies, and talk more about their design and construction.
Check out more of Alastair and Carbon Art 45's work here.